SHAPE is currently developing a 37-acre city centre with parks, plazas, entertainment, and culture at an unprecedented scale. It is evolving into Canada’s largest shopping, dining, residential, and social destination. They call it the City of Lougheed!
Located in Burnaby, the master plan consists of 20 residential towers (+10,000 new homes) and commercial development (entitled for more than 4 million SF). Phase 1 of the project, designed by GBL Architects, provides 1,539 new homes in four concrete structure residential towers over an eight-floor parking and retail structure.
An ever-increasingly complex and fast-paced construction environment, like City of Lougheed, requires a high level of coordination between all players involved. To tackle this challenge, SHAPE retained CadMakers’ Digital Construction Twin services to help identify risks during the design phase, as well as provide on-going coordination support during construction with the general contractor ITC Construction Group (ITC) and their subcontractors.
Pre-construction Phase
As part of CadMakers’ process, the Digital Construction Twin model was built based upon the 2D Contract Documents and specs provided by the design team and the available shop drawings from subcontractors. CadMakers focused on studying the consultant’s design intent while following construction sequencing and practices as seen on site. This allowed CadMakers to relay accurate information of potential risks ahead of actual construction. The robustness of the 3D model helped identify issues regarding low headroom clearances, piping and HVAC routing, and floor slopes and ramps to name a few. These questions prompted coordinated design adjustments that reduced or eliminated the delay time on site when construction is underway.
CadMakers’ 3D model was also shared with the consultant team using our web-based cmBuilder.io platform. cmBuilder was utilized to provide seamless access to the latest model, as well as study the site schedule and logistics with the project stakeholders. For this project, IFC files were also exported for other consultants to use as reference.
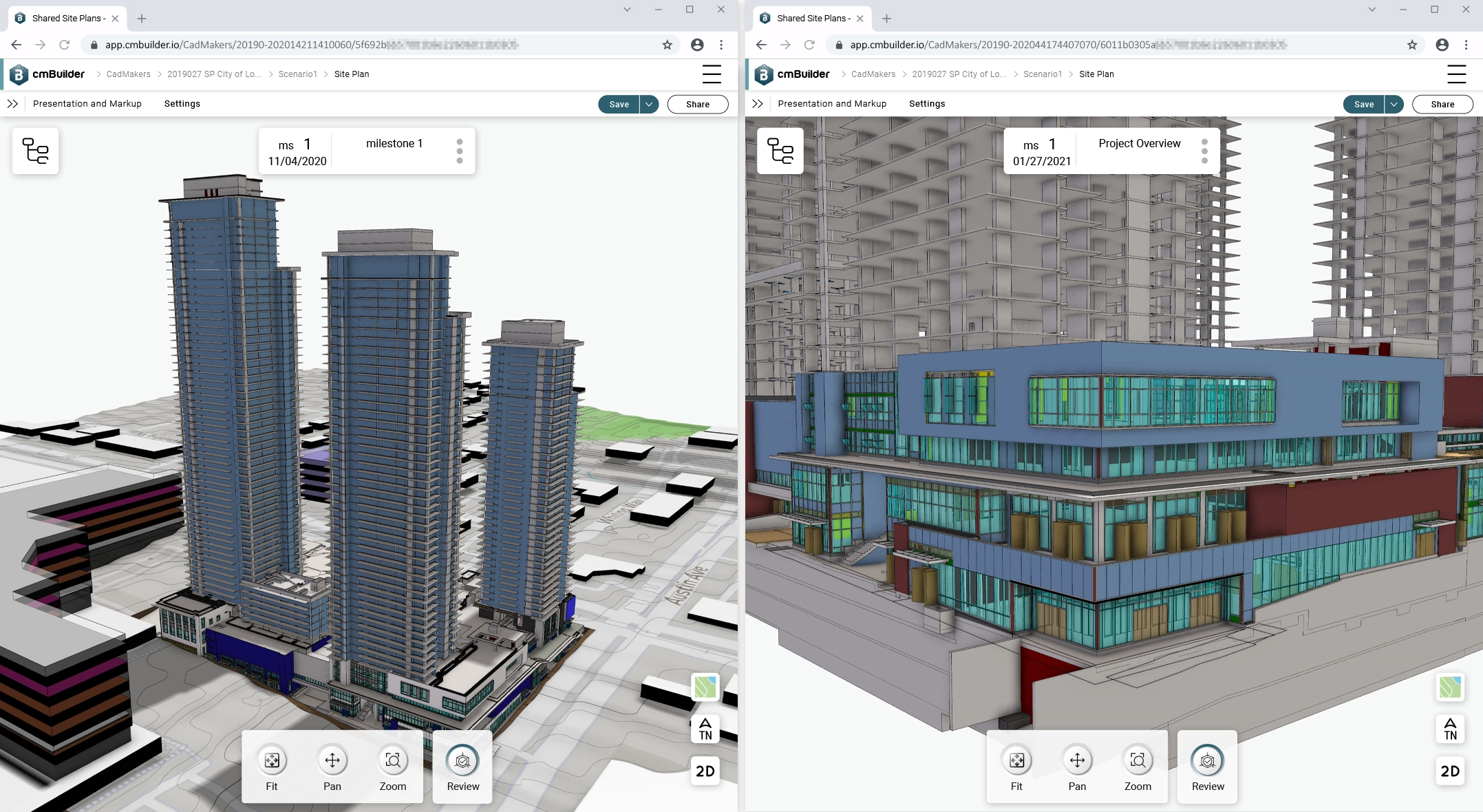
Occupancy schedule
Public access and safety are important to the city. When planning occupancy schedules for each tower, CadMakers visualized for ITC various milestones of the construction stage as well as impact on public realm with the help of detailed 3D images and the 4D construction simulation functionality of cmBuilder.
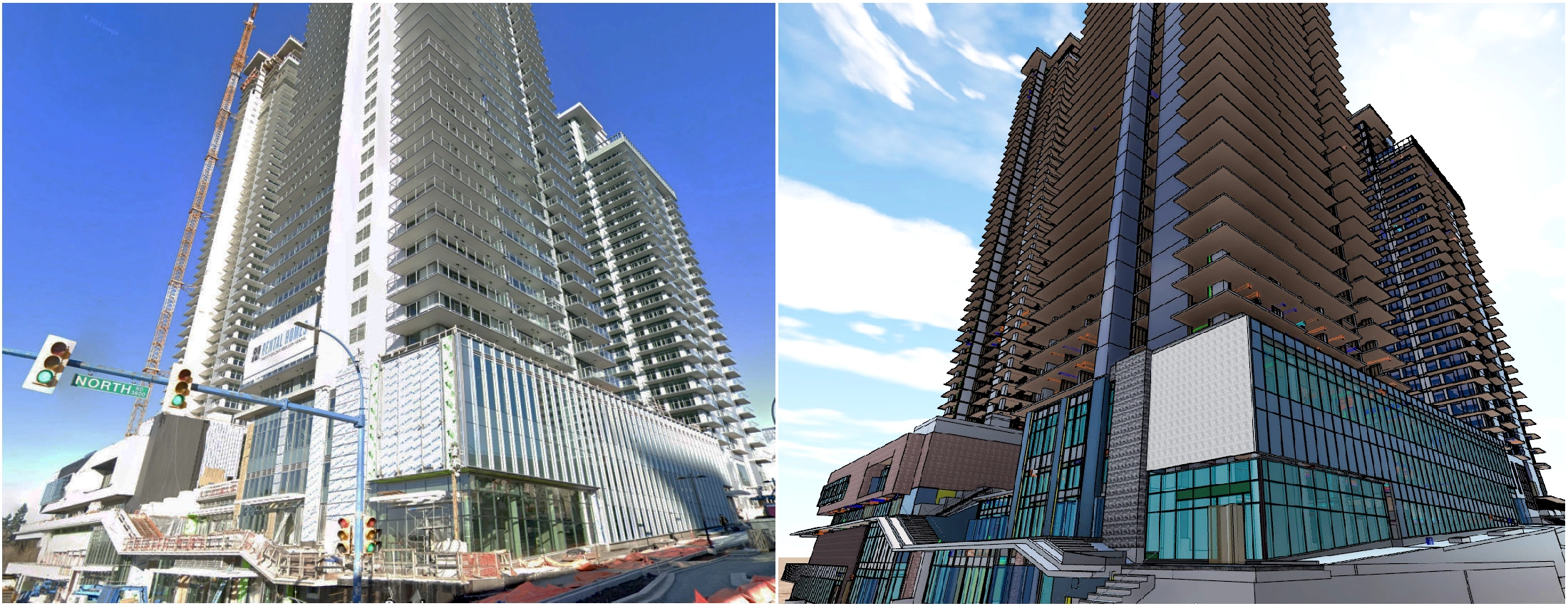
Having an all-in-one coordinated 3D model was a big advantage for all parties involved. It provided not only early identification of conflicts, but also enhanced visualization for the whole team. Some 3D model visualization available through cmBuilder includes mechanical routing, architectural features, ceiling heights, and finalized interior and exterior designs. These features provided the project team with the tools required to make efficient decisions.
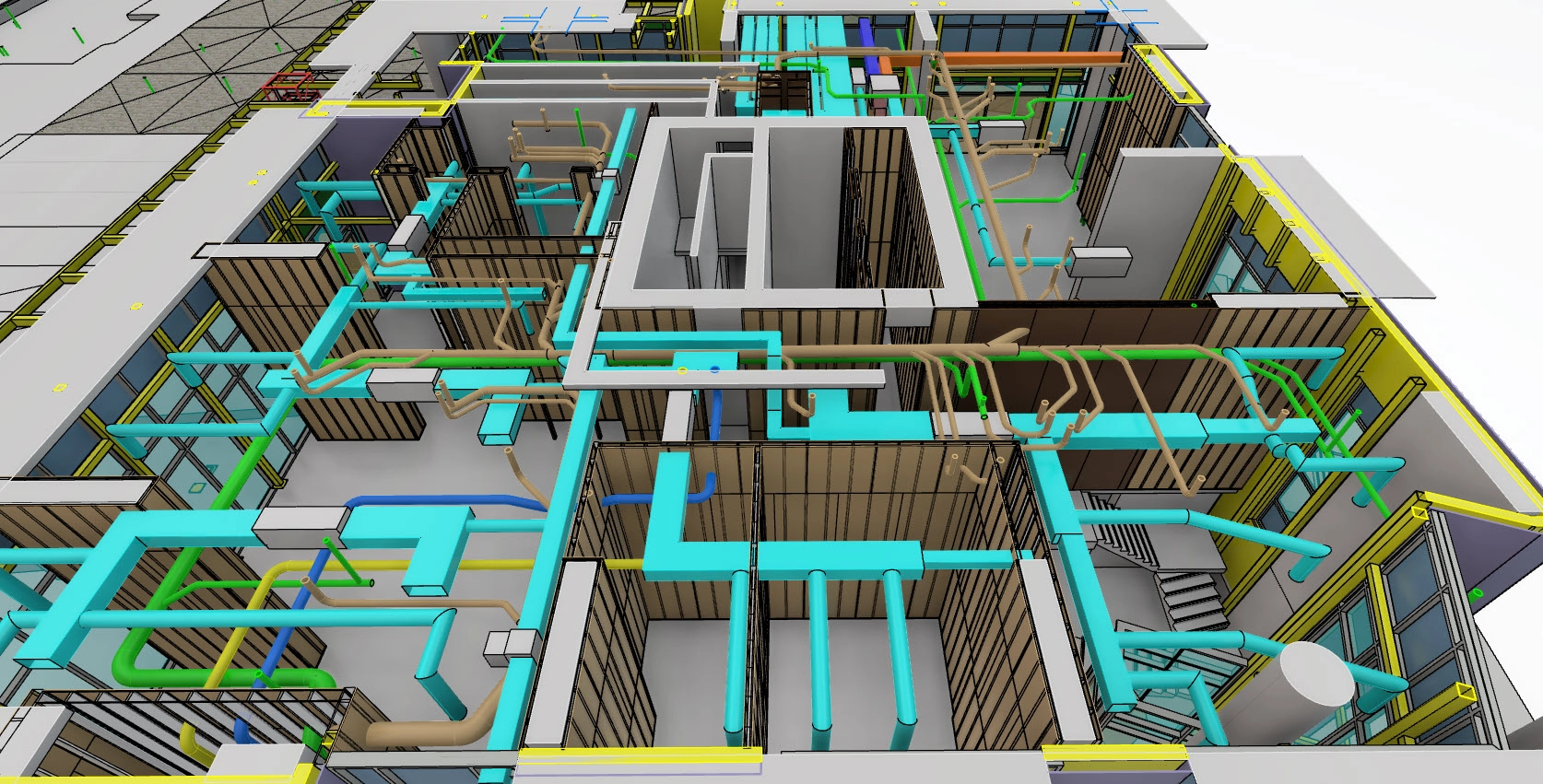
Construction Phase
CadMakers continued to provide support to the project team during the construction phase of the project. Having an updated 3D model on hand during coordination meetings was a powerful tool to communicate the installation sequence to the subcontractors as well as in discussing project risks. Not only was visualizing their own work in 3D helpful in the design stage, but the coordination with other disciplines allowed the consultants to understand the downstream impact of their design.
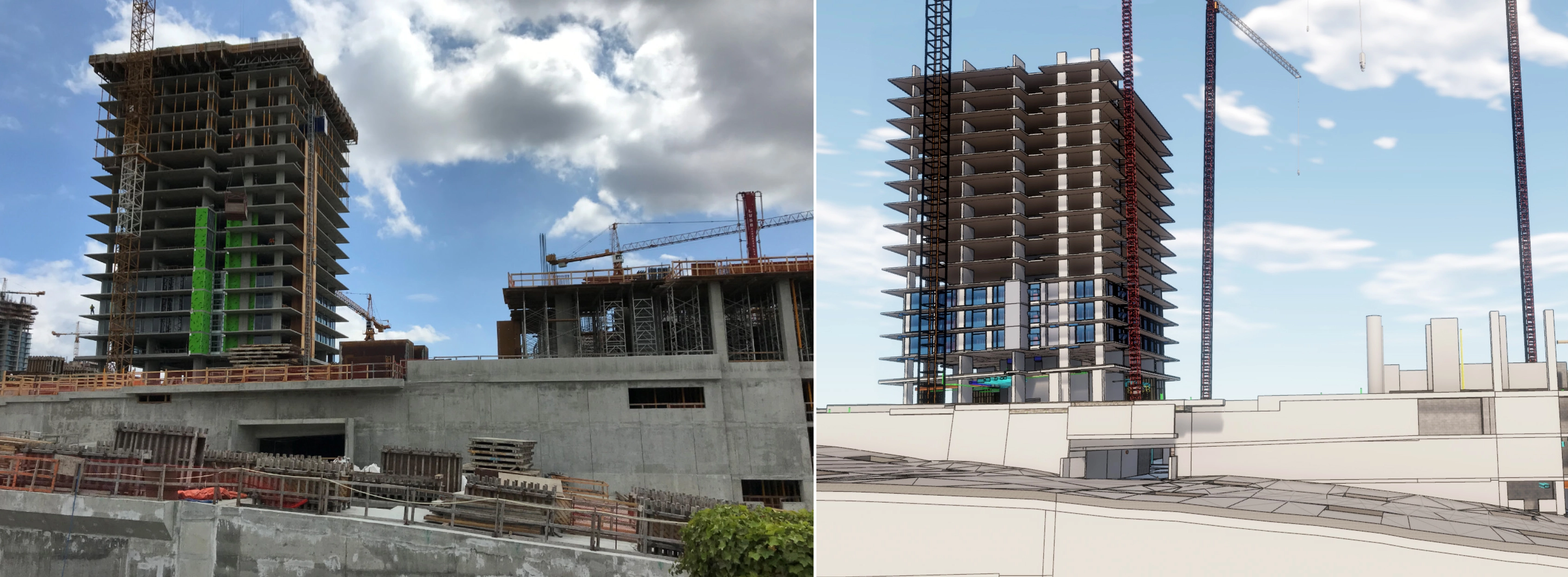
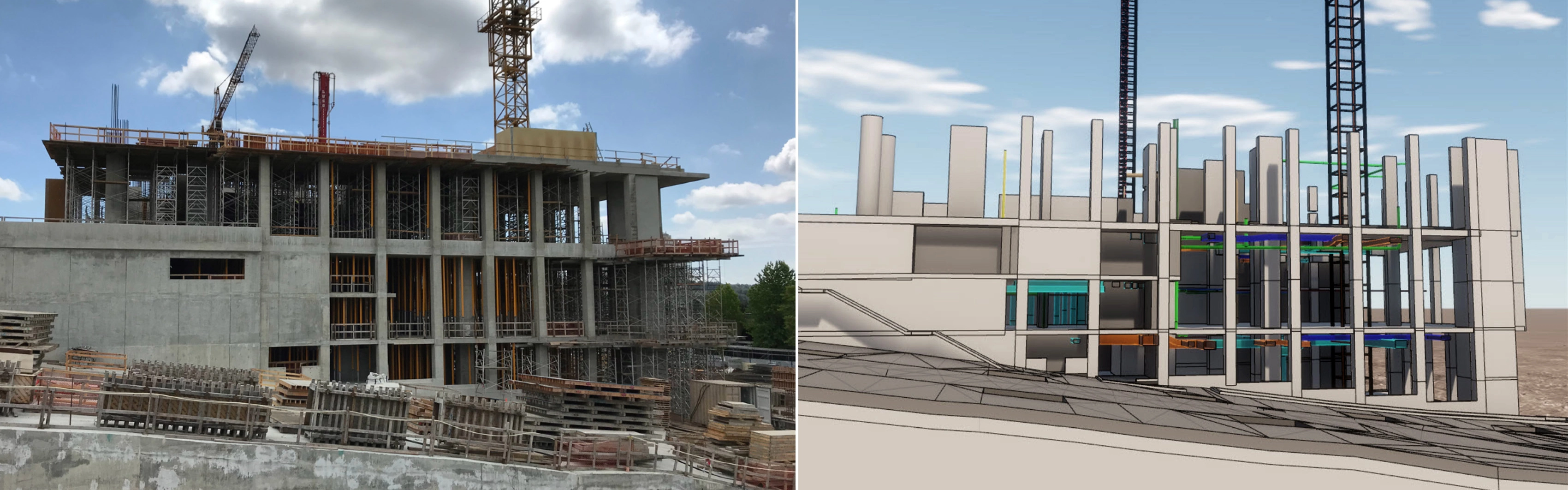
Coordination of embeds and louvers
Phase 1 (first four towers) has a complex façade made of angled and overlapping curtain wall panels. CadMakers provided reviews of the façade shop drawings with exact positions of all the required embeds. Ensuring the embeds were coordinated with the other elements in the concrete structure was crucial, since the embeds were installed months before the actual fabrication of the curtain walls. Coordination of the hundreds of HVAC ducts connecting to outside air with louvers was also important in the review of the envelope design.
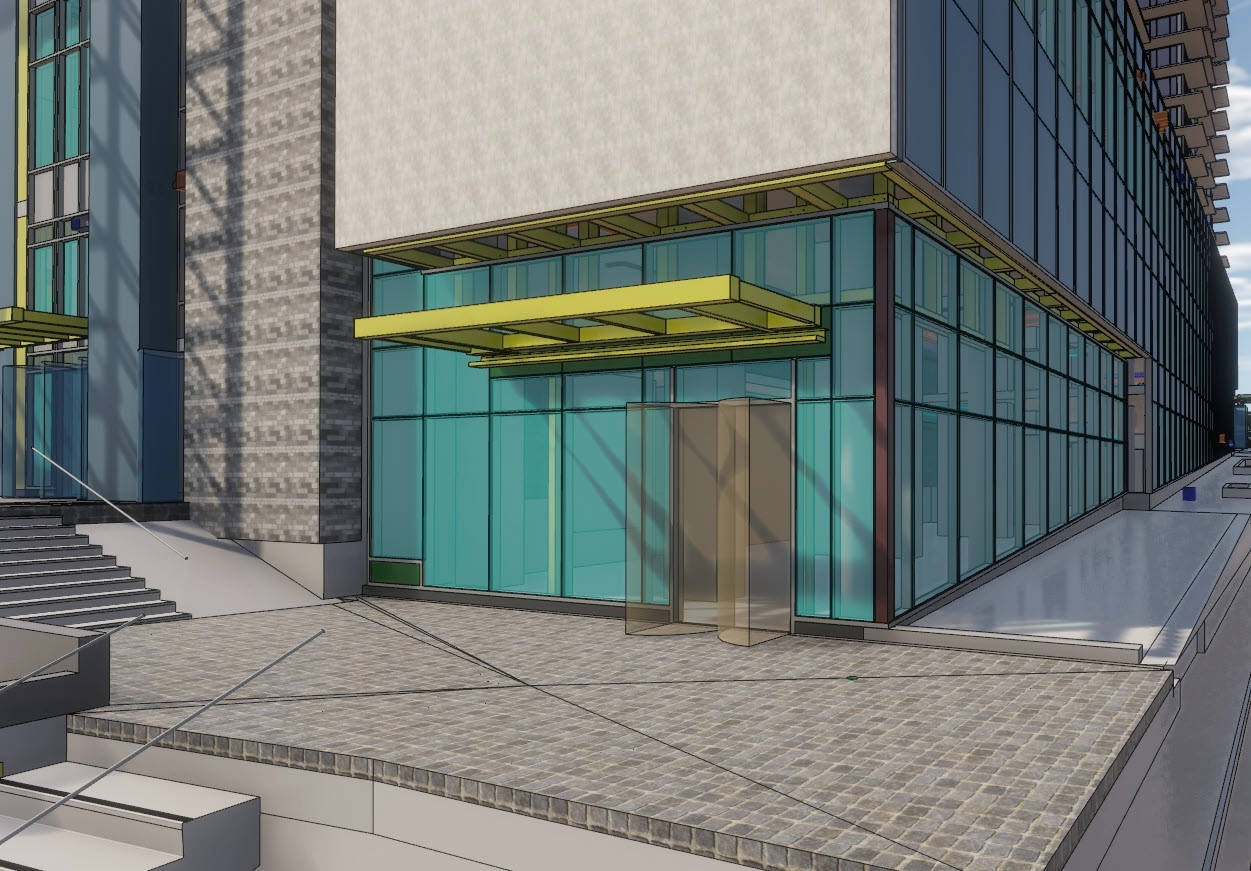
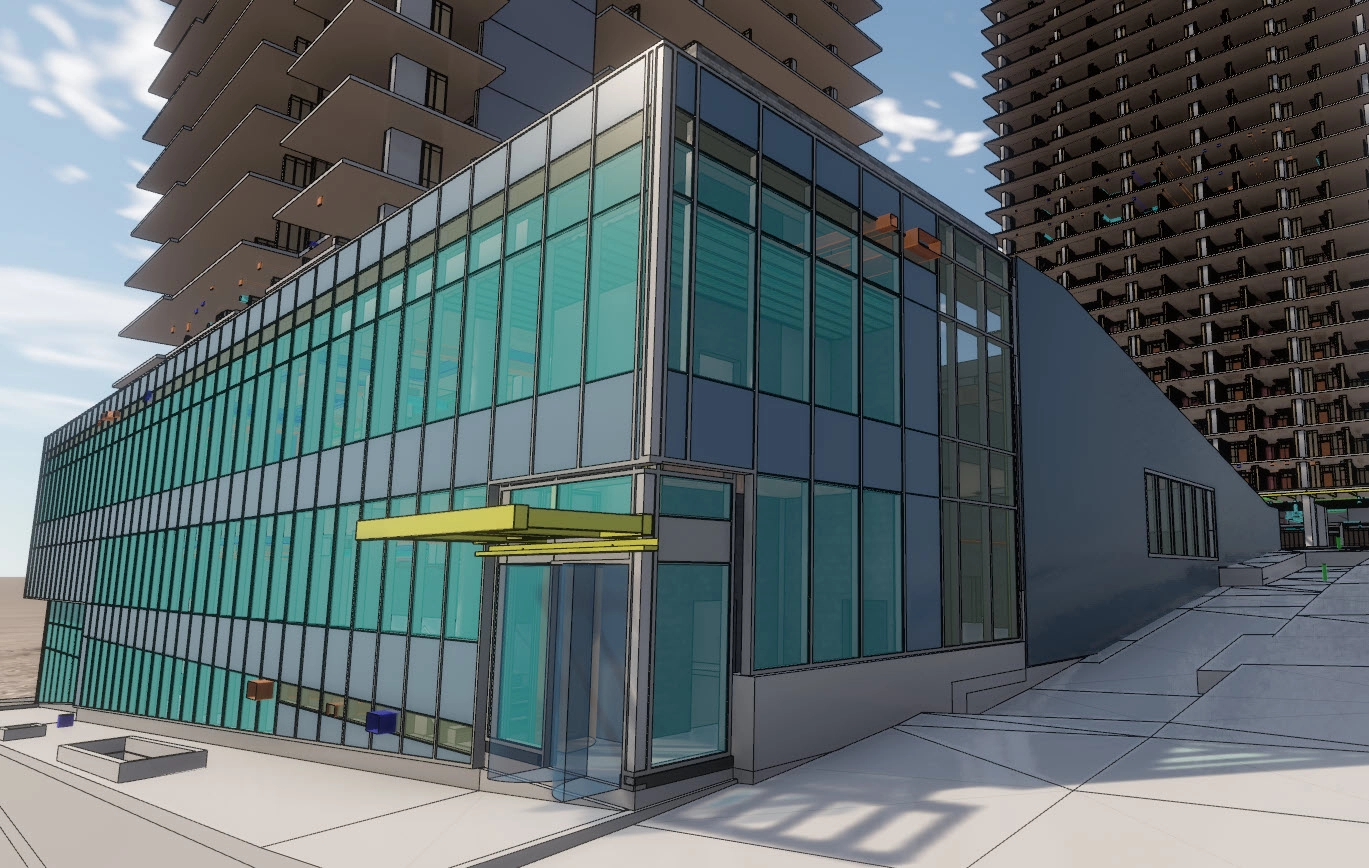
Coordination for fabrication and install of tower envelope
After studying the requirements by the curtain wall fabricator, it was determined that four inches of clearance space was required behind concrete walls for proper installation. Therefore, prior to pouring concrete on site for the tower levels, the position of certain structural walls had to be moved. A modification of that scale, after the fact, would have led to significant cost and schedule impacts.
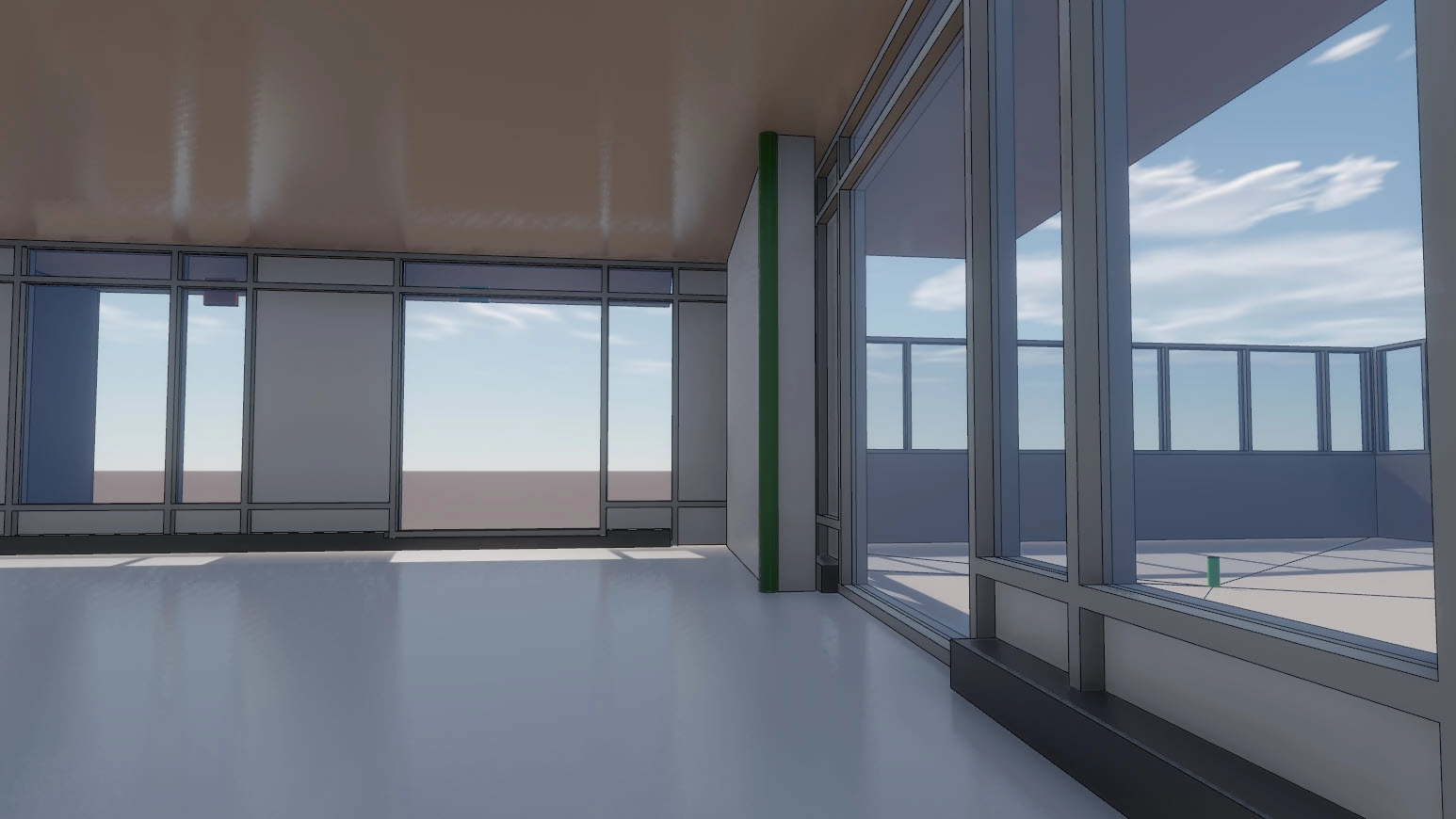
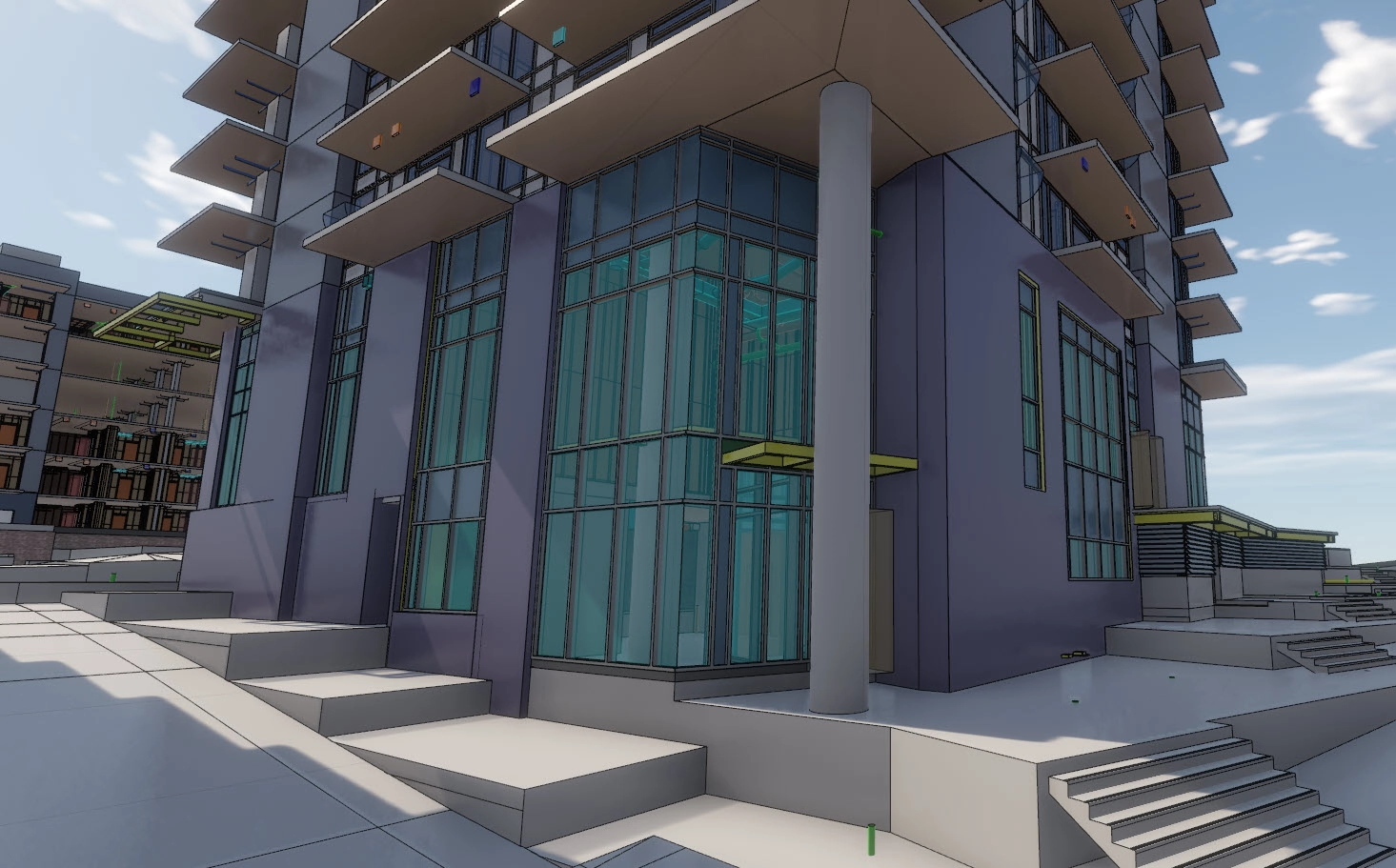
Coordination of fire protection system
Once CadMakers completed their study of the parking structure, it was determined that the headroom clearance on one of the parking floors was insufficient. Considering the minimum required clearance, the placement of the fire protection system (sprinklers) would be below that height requirement. Based on this finding, the consultants made an early decision to adjust the concrete slopes and change the sprinkler heads locally to a side-spraying, wall mounted system.
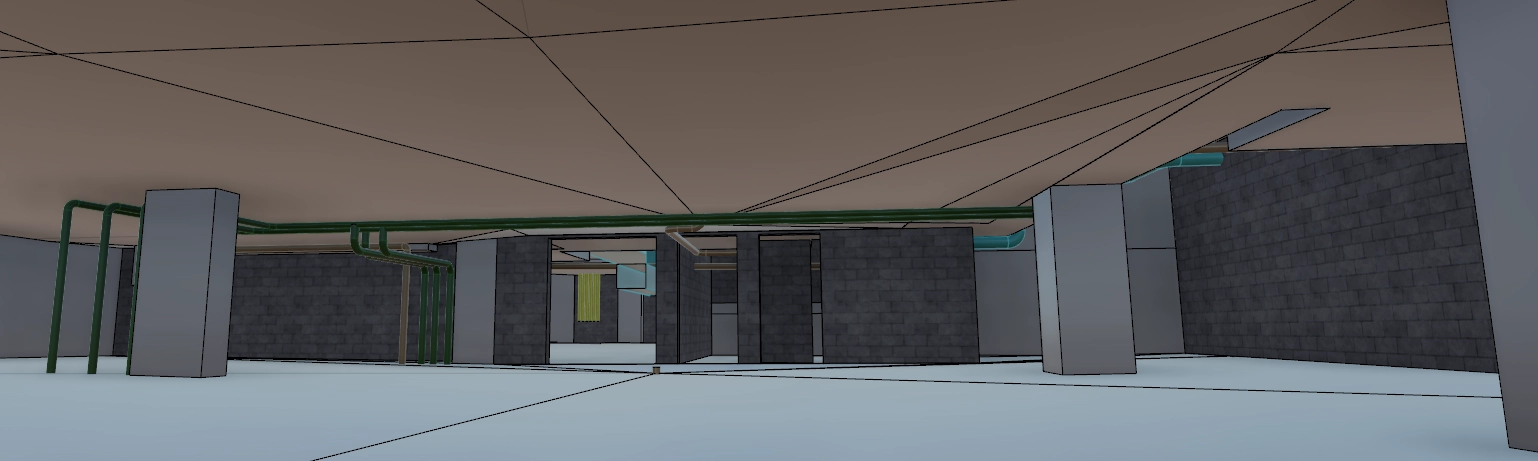
The Digital Construction Twin solution provided by CadMakers helped ITC to communicate early design constructability issues and allowed the consultants to mitigate them. Adjusting work during the construction phase can be time consuming and costly with impacts to the delivery schedule. Additionally, by utilizing cmBuilder and the scheduling/planning capabilities it provides, SHAPE was able to accurately confirm their occupancy schedule during the pre-construction phase.